 |
|
|
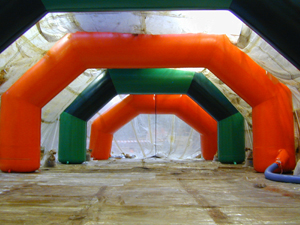 |
|
Conservation project of the Aeromodeller (2006)
creator(s) S.M.A.K., Ghent
contributor(s) ICN, The Netherlands
THE AEROMODELLER CONSERVATION PROJECT
The goals of this intervention were:
1. Conservation of the original artwork.
For a combination of reasons after years of travelling, some seams broke and several old repairs needed urgent treatment. During the exhibition in Madrid (2002), one large construction seam opened and the balloon could not hold its form anymore.
A meticulously planned conservation project was carried out by the Conservation Department of the S.M.A.K. museum. Different stages of treatment and scientific analytical research were set up. For the scientific analytical research segment of this conservation project, a cooperation agreement was established with the Netherlands Institute for Cultural Heritage (ICN) in late 2003.
The scientific analytical research focused on:
— characteristics of the original materials
– condition of the artwork
– type of treatment
– effect of the treatment on the materials
2. Sharing the results of the intervention and the scientific analytical research with the international conservation community.
Very few resources were found dealing with synthetic adhesives and the characteristics and conservation of plasticized PVC. Publications were issued to communicate the results of this investigation.
3. Preparing the artwork for being loaned out and travelling, i.e. facilitating assembly and disassembly, preventing exposure and ensuring transport under optimal conditions.
WORKING ENVIROMENT / SUPPORT SYSTEM
To be able to start working and investigating, a sufficient working space was set up. We came up with the idea of using inflatable forms – or ‘bows’ – to support the piece from the inside. Five air bows were installed and, due to this construction, the balloon itself did not need to be inflated. The air bows were made in three different sizes, the large one being placed in the middle of the balloon. The air bows were supplied with air by two ventilator motors forcing air through separate flexible hard plastic tubes connected to each of the bows.
To facilitate entering the balloon, the two ends were opened. To open these ends, two PVC sections had to be removed, one at the front end and one at the back end. This was possible because the old adhesive had lost its original strength.
With this supporting structure, work could be done on the outside and inside of the balloon. It was obvious that research and treatment required a suitable working environment, so the balloon was installed in a huge hall, which was heated though not acclimatized. Treatment could be carried out both on the inside and on the outside of the balloon. Once the sides were treated, the air bows were taken out and the balloon was rotated approximately 2 meters further. Each time, work was done on 1.5 meters of the surface, and the balloon was rotated approximately seven times until the cleaning of the entire surface was complete.
OBSERVATION OF THE ARTWORK
The zeppelin was originally assembled from two main sections, connected along a large vertical (circular cross-section) seam in the middle. Horizontally,15 bands of PVC film were adhered by synthetic rubber adhesive, coming together at the front and back ends of the balloon.
In the recent conservation project, the balloon was analysed to determine its structure, its characteristics and its form. It had originally been divided by the artist into 10 vertical sections with thin bands of PVC film adhered on the surface of the balloon for aesthetic reasons. The resulting10 vertical and 15 horizontal bands divide the balloon into 150 different zones. Drawings and schematic diagrams were made with a coordinate grid numbering system to identify each individual zone for purposes of study.
Today there are 45 suspension points: 23 on one side and 22 on the other side. In the literature, 52 suspension points are mentioned. It is possible that some points have been removed down through the years.
English
Attribution Non-commercial
|